GN Stack Vibrating Screen is mainly suitable for wet screening, classification and dehydration treatment of fine-grained materials in mineral processing, coal preparation and other industries. It can be set to 2 to 5 layers according to on-site requirements. GN Stack Vibrating Screen is a self-developed product of GN company. It is designed and driven by a single vibration source (dual vibration motor) by using the principle of two-degree-of-freedom resonance to realize linear vibration of the whole machine. GN Stack Vibrating Screen has unique vibration mode, energy saving, high screening efficiency, large processing capacity, advanced technology, simple structure, stable and reliable operation, and is currently one of the most advanced equipment in the field of fine-grained material screening. GN Stack Vibrating Screen adopts Polyurethane Screen Mesh, with high opening rate (28-45%) and average life span of more than 6 months.
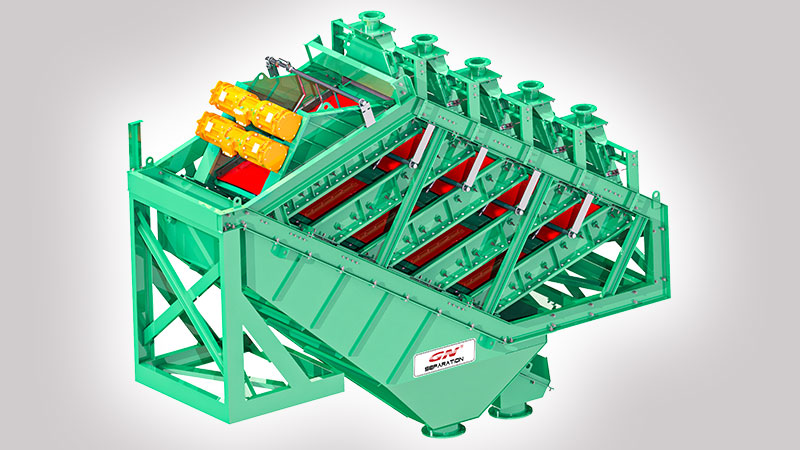
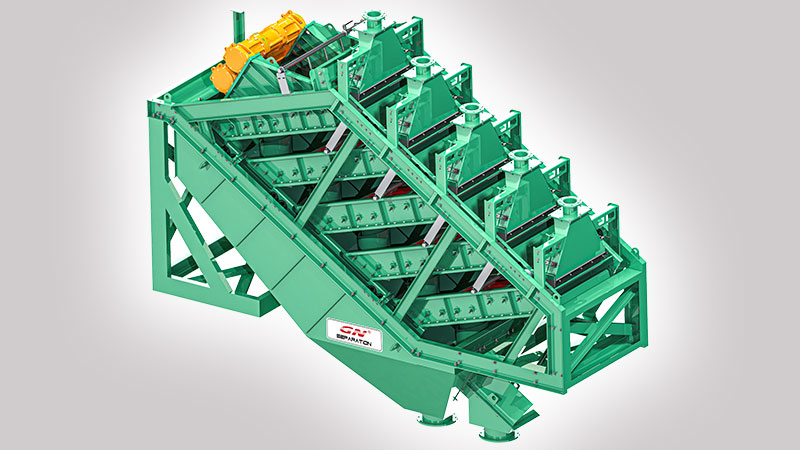
Stack Vibrating Screen-Fine Sizer - Small and Medium Size Models Technical Parameters
Model | GND3Z1014 | GND4Z1014 | GND5Z1014 | GND2Z1021 | GND3Z1021 | GND4Z1021 | GND5Z1021 |
Screen box layers |
3 |
4 |
5 |
2 |
3 |
4 |
5 |
Total screening area |
4.2㎡ |
5.6㎡ |
7㎡ |
4.2㎡ |
6.3㎡ |
8.4㎡ |
10.5㎡ |
Linear vibration amplitude (double) |
1-2mm |
Total installed power (output) |
2sets×1.84kW |
Vibration frequency |
25Hz |
Screen inclination |
17.5° |
Mesh size |
0.045- 2mm |
Screen size (L×W) |
700×1050(mm) |
Number of screen |
6 |
8 |
10 |
6 |
9 |
12 |
15 |
Processing capacity (Dry ore m3/h) |
6~18 |
8~24 |
10~30 |
5~12 |
6~19 |
8~25 |
10~32 |
Remark |
- The above parameters are for reference only and can be adjusted according to the customer's situation. Finally the quotation and technical agreement shall prevail.
- Regarding Stack Vibrating Screens of the same size for different material requirements under different working conditions, the processing capacity varies greatly. For details, please consult GN.
|
The above specification and parameters for reference only. |
Stack Vibrating Screen-Fine Sizer - Medium and Large Size Model Technical Parameters
Model | GND3Z1416 | GND4Z1416 | GND5Z1416 |
Screen box layers |
3 |
4 |
5 |
Total screening area |
6.72㎡ |
8.96㎡ |
11.2㎡ |
Linear vibration amplitude (double) |
1-2mm |
Total installed power (output) |
2sets×1.84kW |
2sets×2.3kW |
Vibration frequency |
25Hz |
Screen inclination |
17.5° |
Mesh size |
0.045- 2mm |
Screen size (L×W) |
840×1450(mm) |
Number of screen |
6 |
8 |
10 |
Processing capacity (Dry ore m3/h) |
8 ~ 25 |
11~33 |
14~42 |
Remark |
- The above parameters are for reference only and can be adjusted according to the customer's situation. Finally the quotation and technical agreement shall prevail.
- Regarding Stack Vibrating Screens of the same size for different material requirements under different working conditions, the processing capacity varies greatly. For details, please consult GN.
|
The above specification and parameters for reference only. |
Stack Vibrating Screen-Fine Sizer Features
- GN Stack Vibrating Screen is designed with dual-motor self-synchronization principle, and the screen box assembly moves linearly.
- Imported vibration motor (Martin motor or OLI motor) with advanced technology, reliable operation and long trouble-free operation time.
- The screen box general assembly of the Stack Vibrating Screen is arranged in multiple layers. Compared with similar vibrating screen, it has the advantages of small footprint, large processing capacity per unit area, high screening efficiency, low power consumption, small dynamic load, simple operation, stable performance, safety and durability, low maintenance and so on.
- The Polyurethane Screen Mesh is used, which has good elasticity and is not easy to be blocked. Two to three screens can be installed in the each single-layer screen box.
- The screen is fixed by pulling-bolt components, which is easy to operate and reliable to fasten.
- The surface treatment of the vibrating screen adopts the sandblasting process, and the heavy anti-corrosion paint is used for spraying, which has good anti-corrosion performance. The contact surface with the material adopts the form of spraying polyurea resin wear-resistant anti-corrosion layer to protect the surface of the screen and prolong the service life of the screen.
Stack Vibrating Screen-Fine Sizer Main Components
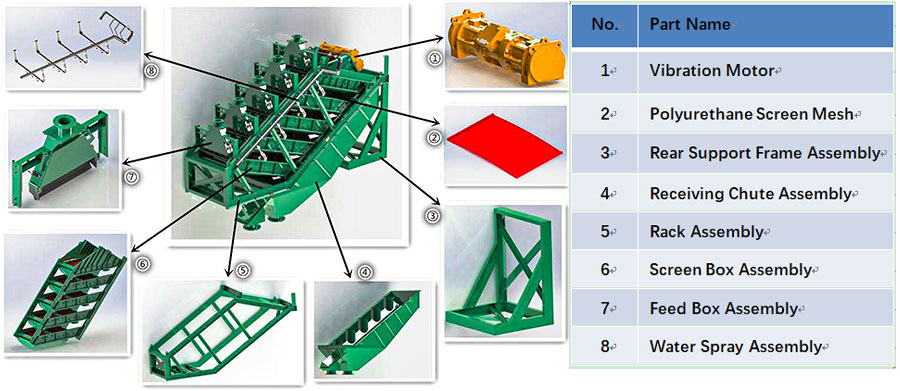
Feeding Box Features of GN Stack Vibrating Screen-Fine Sizer
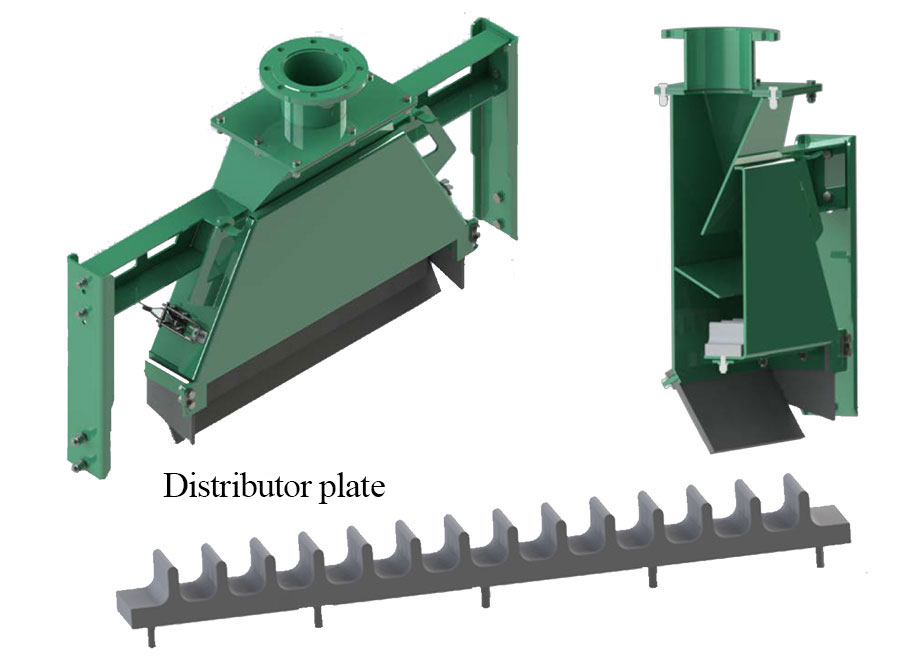
- The feeding box adopts a unit-combination structure, and bolts are used between each unit, or the form of quick clamping is used to combine them together. It is easy to assemble and disassemble, and it is convenient for on-site cleaning and replacement of the feeding box unit. When a part is broken, only the broken parts need to be replaced, reducing maintenance costs and saving resources.
- There are multi-level buffer steel plates and material distribution plate buffers inside, which slows down the flow of materials, increases the life of the feeding box, slows down the discharge speed of the feeding box, slows down the impact on the screen, increases the life of the screen, and reduces the damage of the screen. Reduce production and maintenance costs.
- A material distribution board is installed at the lower part of the general assembly of the feeding box, so that the materials are evenly distributed in the feeding box and evenly distributed on the screen, so as to increase the screening efficiency of the vibrating screen.
- The inner side of the general assembly of the feeding box is sprayed with polyurea resin, so that the feeding box has better wear resistance and corrosion resistance, and has a longer life.
- The height of the feeding box can be adjusted by adjusting the positions of the mounting holes on both sides to achieve three-level adjustment to find a height that is suitable for on-site working conditions.